Chemical processes in electroplating plants often produce harmful exhaust air emissions.
An effective exhaust air system is therefore essential to protect the environment and ensure the health of employees and residents.
CALORPLAST Wärmetechnik offers customized solutions for recovering the heat contained in the exhaust air, which have been specially developed to meet the requirements of the electroplating industry.
Our innovative plastic heat exchangers combine high efficiency with complete corrosion resistance and thus contribute to the sustainable and economical operation of your plants.
What role does the heat exchanger play in the exhaust air system of an electroplating plant?
A heat exchanger is a central element in the exhaust air system of an electroplating plant.
It is used to recover the heat contained in the exhaust air and feed it back into the heat cycle.
In most cases, this is done by preheating the incoming outside air, but it can also be used with other concepts.
This not only reduces energy consumption, but also contributes to lower operating costs.
Our gas-water heat exchangers and the Evolution series are specially developed for these tasks and offer maximum performance and reliability, even in the aggressive working environment of electroplating plants.
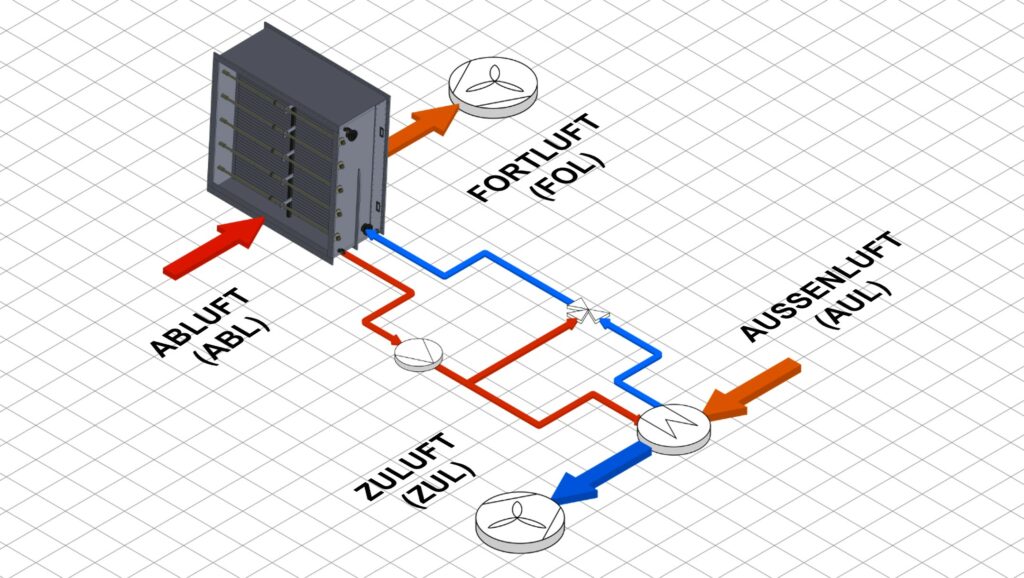
Corrosive exhaust air? More than a waste product!
Energy recovery
Energy recovery is a major advantage of using heat exchangers in electroplating plants.
As several tens of thousands of cubic meters of exhaust air have to be extracted per hour, depending on the size of the plant, this results in enormous heating costs, especially in the cold season.
Depending on the process and system, this proportion is approx. 7 – 20% of the total energy requirement of the plant.
[1] With our heat exchangers, 50 – 70% of this waste heat can be reused.
The most commonly used concept is feeding it into the fresh air heat exchanger by means of a circulation system.
Alternative concepts involve feeding the recovered heat into a liquid circuit in conjunction with a heat pump.
This means that the energy potential can also be used all year round, or alternative forms of heating for process tanks or storage tanks can be realized.
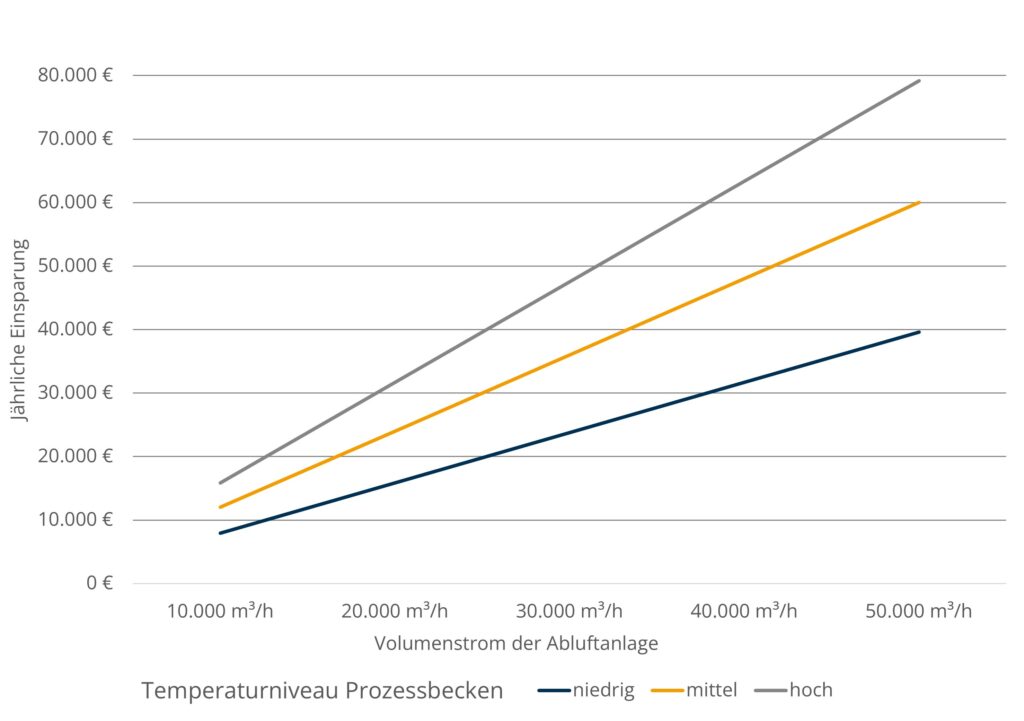
Sustainability
Sustainability is a key aspect of our solutions.
By making efficient use of waste heat and reducing energy consumption, our heat exchangers contribute to more sustainable and future-proof production.
This not only supports your environmental goals, but also offers long-term economic benefits.
Sustainable practices are an important competitive factor today and can help you stand out from the competition.
Our heat exchangers are made entirely of plastic, which reduces maintenance intervals and increases the service life enormously.
This not only reduces operating costs, but also minimizes the environmental footprint of your system.
By using high-quality materials and advanced manufacturing processes, we ensure that our heat exchangers meet the highest efficiency standards in terms of performance and sustainability.
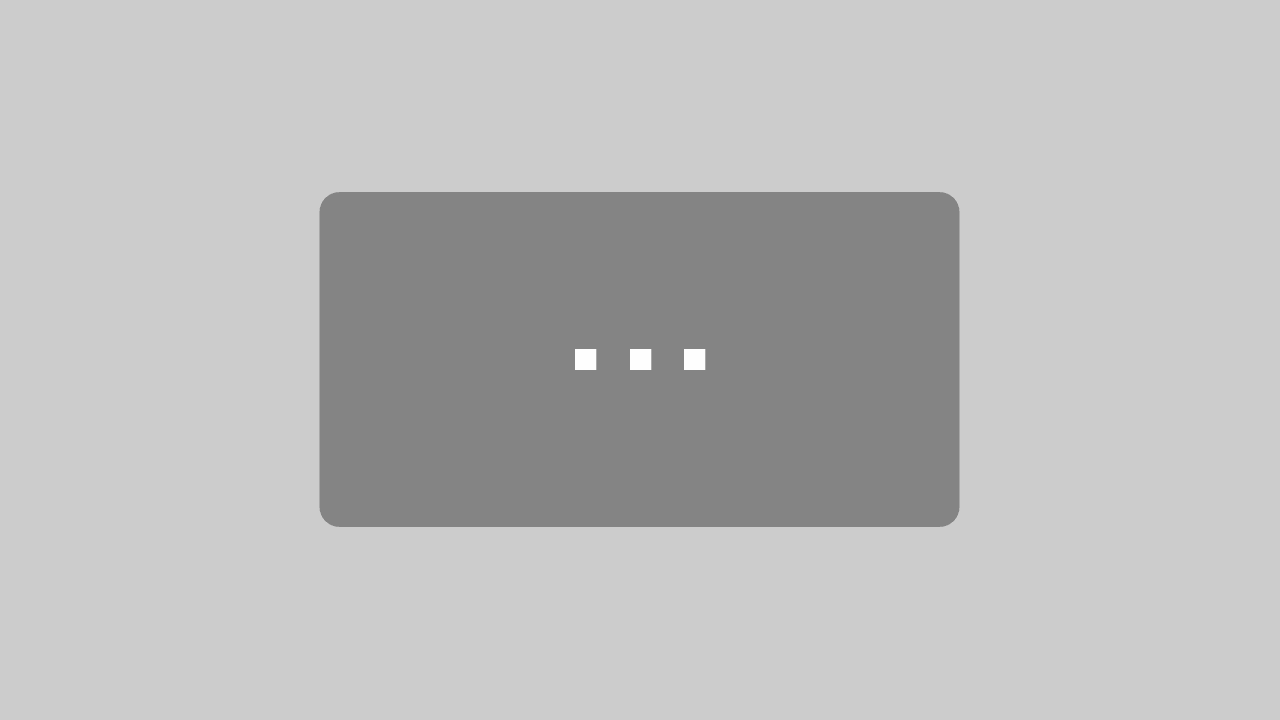
Mit dem Laden des Videos akzeptieren Sie die Datenschutzerklärung von YouTube.
Mehr erfahren
Are you looking for heating technology for your electroplating company?
Characteristics
Operating temperature
Our heat exchangers are designed for a wide temperature range of different galvanic processes and offer reliable performance under extreme conditions.
Operating temperatures vary by model and application, but all our products are designed to handle high temperatures and aggressive media.
The ability to operate in a wide range of temperatures makes our heat exchangers particularly flexible and versatile.
With over 40 years of experience in surface technology and electroplating, we have the necessary knowledge to support you in the planning and implementation of your heat recovery.
From hot-dip galvanizing to nickel plating, hard chrome plating and anodizing systems, our gas-water heat exchangers perform reliably at all temperatures and in all climate zones around the world, reducing operating costs and CO2 emissions.
Material selection
Choosing the right material for a heat exchanger is crucial to its performance and longevity.
Most of our gas-water heat exchangers are made from high-performance polyethylene (PE).
We use the PE-RT(raised temperature) variants, which have higher strength even at higher temperatures and have proven particularly effective in highly aggressive environments.
Our Evolution series uses PE-HD(high density), which makes it lightweight and flexible.
At the same time, our Evolution series achieves the highest efficiency classes in line with modern European standards.
These materials are combined with other engineering plastics such as PP, PPs or PVDF as required to meet your requirements.
By using these high-quality materials, we ensure that our heat exchangers offer excellent performance and a long service life.
Our experts will be happy to help you select the right material for your specific requirements to ensure the best possible efficiency and durability.
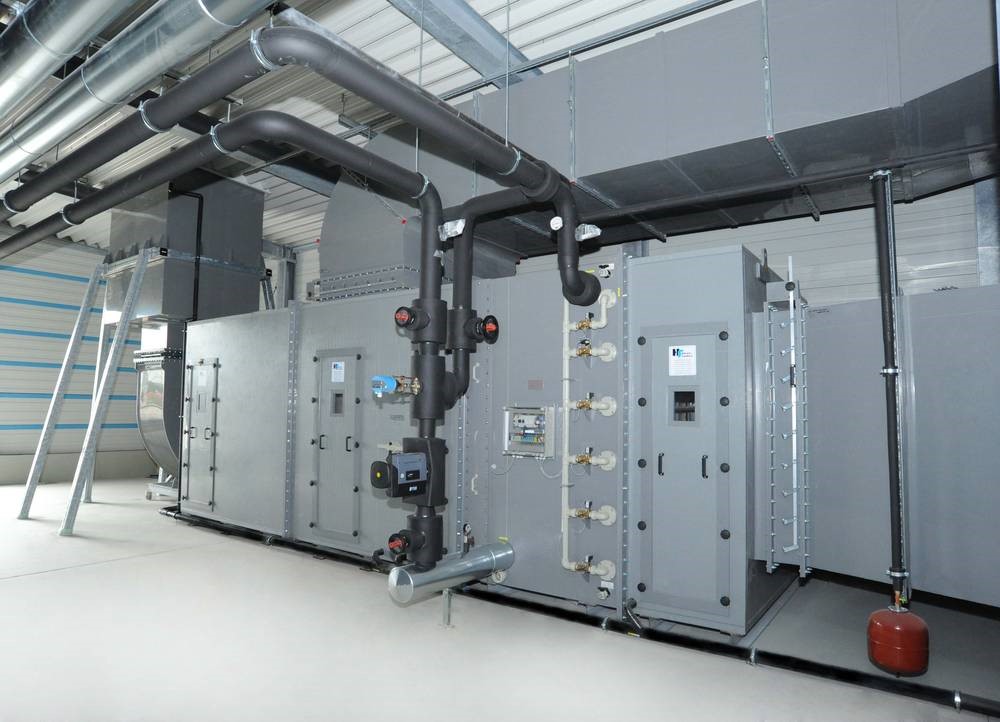
Areas of application
Our heat exchangers are used in various areas of electroplating.
They are ideal for recovering heat from exhaust air flows, cooling process fluids and controlling temperatures in sensitive production processes.
Their versatility and high performance make them an indispensable component in modern electroplating systems.
In addition to electroplating, our heat exchangers can also be used in other industries that have similar requirements for exhaust air purification and heat recovery.
These include the chemical industry, laboratories in schools and educational establishments, as well as semiconductor production.
Our heat exchangers offer reliable performance in all these areas and help to increase efficiency and reduce costs.
Other relevant characteristics
In addition to the properties mentioned above, our heat exchangers offer high corrosion resistance, low maintenance requirements and easy integration into existing systems.
These features make them a reliable and cost-effective solution to the challenges of exhaust air purification and heat recovery in electroplating operations.
Our heat exchangers have a modular design, which makes it easy to adapt them to the specific needs of your system.
This not only facilitates installation, but also on-site maintenance.
The use of advanced manufacturing techniques ensures that our heat exchangers meet the highest quality standards and offer long-term performance.