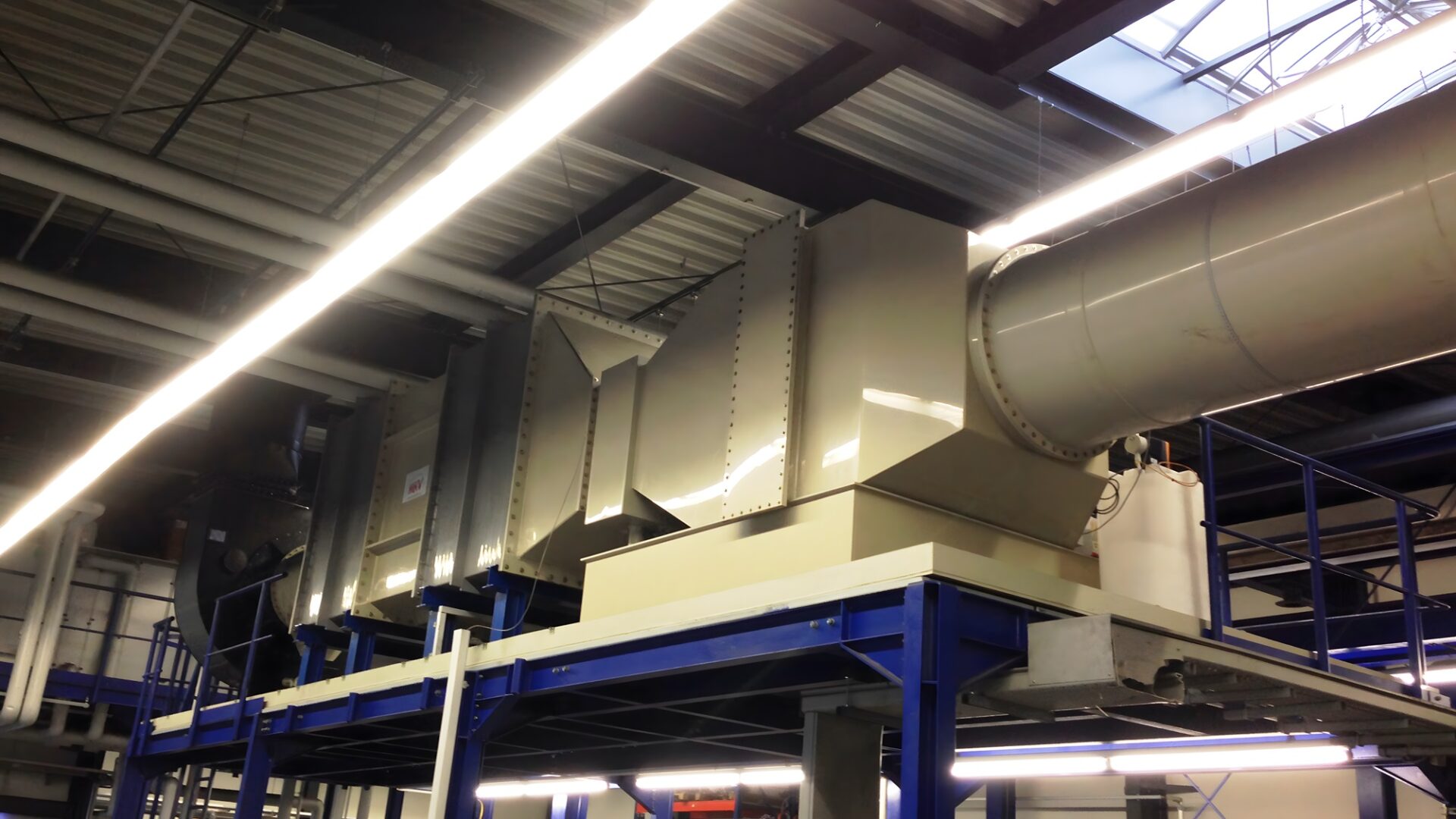
Abluftreinigung in der Galvanik
Die Abluftreinigung in der Galvanik ist ein entscheidender Prozess, um Umwelt- und Gesundheitsschutz zu gewährleisten und die Betriebskosten durch Wärmerückgewinnung zu senken.…
Startseite | Wissenswertes
Die Abluftreinigung in der Galvanik ist ein entscheidender Prozess, um Umwelt- und Gesundheitsschutz zu gewährleisten und die Betriebskosten durch Wärmerückgewinnung zu senken.…
In Galvanikbetrieben entstehen durch die chemischen Prozesse oftmals schädliche Abluftemissionen. Eine effektive Abluftanlage ist daher unerlässlich, um die Umwelt zu schützen und…
Case study Nr. 20: Schwefelsäureverdünnung Ausgangsituation Bei der Herstellung von Batterien werden große Mengen von Schwefelsäure H2SO4 als Elektrolyt benötigt. Die…
Case study Nr. 19: Redox-Flow Batterie Ausgangsituation In der Anwendung als Redox-Flow Batterie ist Vanadium in Schwefelsäure gelöst und besitzt dort…
Case study Nr. 18: Schmuckgalvanik Ausgangsituation In einer Schmuckgalvanik in Spanien sollte eine bestehende Anlage von elektrisch beheizten Becken auf Grund…
Case study Nr. 17: Phosphatierung Ausgangsituation Wenn Grundmaterialien phosphatiert werden sollen, müssen die Becken temperiert werden. Bei dieser Reaktion findet eine…
Case study Nr. 16: Plating om Plastics (PoP) Ausgangsituation Obwohl man Oberflächenbeschichtungen in der Galvanotechnik meist mit der Behandlung von metallischen…
Case study Nr. 15: Bandbeizen Ausgangsituation Bandbeizen werden zur Galvanisierung von Drähten oder dünnen metallischen Platten genutzt. Dabei wird das zu…
Case study Nr. 14: AquaZoo Ausgangsituation Viele Fische und Anemonen mögen keine Metallionen in ihrer Umgebung. Gleichzeitig muss das Süßwasser oder Salzwasser…
Case study Nr. 13: Biogas Entschwefelung Ausgangsituation Bei der Herstellung von Biogas entsteht im Fermenter giftiges und korrosives Schwefelwasserstoffgas, welches dem Gasstrom entzogen…
Case study Nr. 12: Abluftreinigung: Biogastrocknung für große Brauerei Ausgangsituation Biogas ist ein Nebenprodukt der organischen Reststoffverarbeitung in der Tierhaltung, in Brauereien…
Case study Nr. 11: Biogas klein Ausgangsituation Bei der Herstellung von Biogas entsteht im Fermenter giftiges und korrosives Schwefelwasserstoffgas und Ammoniak, welches…
+49 (0)2151 - 8777-12